Mill Grinding Balls, Grinding Cylpebs and Grinding Rods
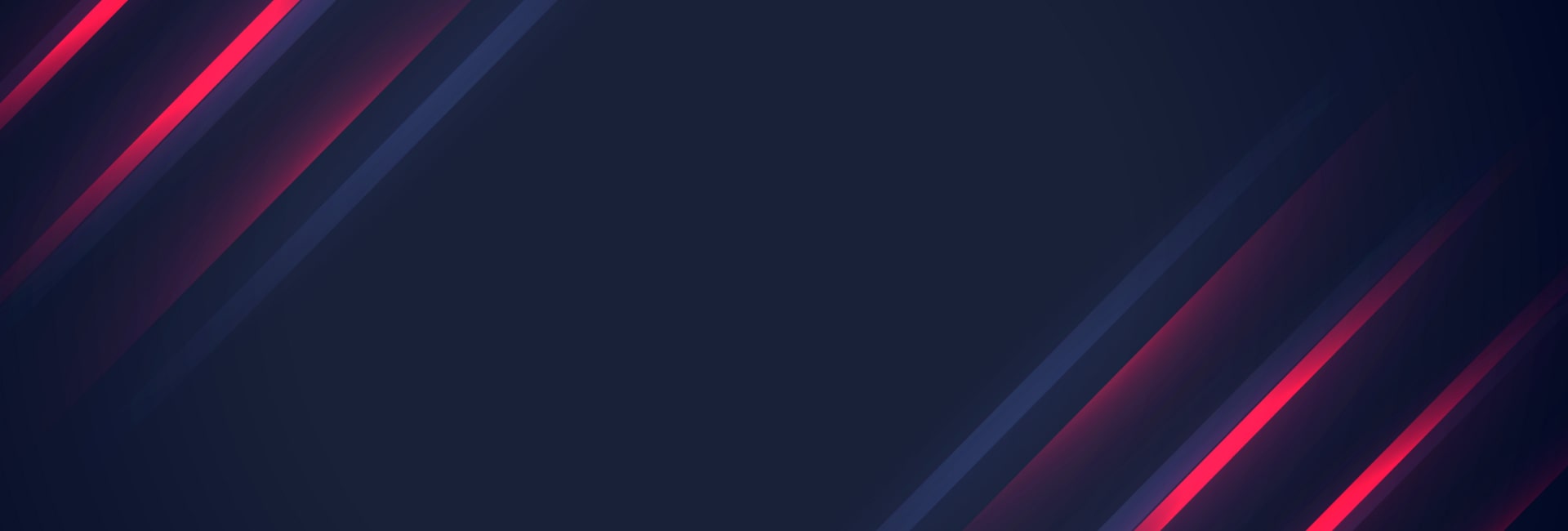
100mm Wear Resistant Steel Grinding Balls – Mill Balls for Mineral Processing Ball Mills
PRODUCT PARAMETERS
- Type: Forged Steel Grinding Balls
- Diameters(mm):100mm, other size available
- Application: mining, cement production, power plants, chemistry industries
- High hardness
- Good wear resistance
- High impact toughness
- Impact value(J/cm²): ≥12
- Diameter roundness(mm): +4,-3
- Roundness: ≤4%
Description
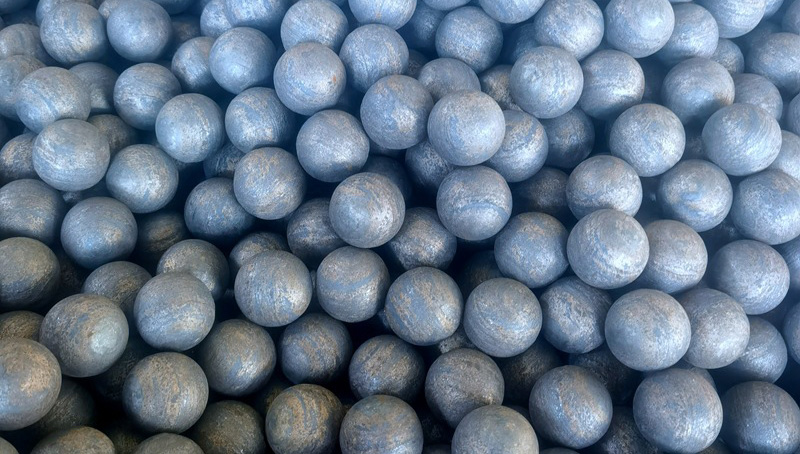
Forged steel balls have high volume hardness, dense structure, and maintain their shape without breaking. They are ideal for grinding operations in industries like metal mining and thermal power plants, especially in semi-autogenous and ball mills
I. Product Overview
Our forged steel balls are manufactured using high-quality alloy steel sourced from leading steel mills. Through fully automated production processes, we ensure precise dimensions, perfect roundness, high hardness, and superior mechanical properties. These steel balls are designed to be wear-resistant, deformation-free, and crack-resistant, making them ideal for demanding industrial applications.
Diameter tolerance and roundness
Diameter | 30 | 40 | 50 | 60 | 70 | 80 | 90 | 100 | 110 | 120 | 125 | 150 |
Diameter roundness(mm) | ±2 | +3,-2 | +4,-3 | +5,-4 | ||||||||
Roundness(%) | ≤2 | ≤3 | ≤4 | ≤5 |
Technical specification
Material Gr. | Breakage rate | Hardness(HRC) | Impact value(J/cm²) | Drop Test | Micro structure |
45# | <1% | ≥45 | ≥12 | ≥8000 | M+C |
60Mn | <1% | ≥55 | ≥12 | ≥12000 | M+C |
65Mn | <1% | ≥58 | ≥12 | ≥12000 | M+C |
70Mn | <1% | ≥60 | ≥12 | ≥12000 | M+C |
40Cr | <1% | ≥55 | ≥12 | ≥12000 | M+C |
70Cr2 | <1% | ≥58 | ≥12 | ≥12000 | M+C |
B-2 | <1% | ≥58 | ≥12 | ≥15000 | M+C |
B-3 | <1% | ≥60 | ≥12 | ≥15000 | M+C |
Chemical composition
Material Gr. | C(%) | Si(%) | Mn(%) | Cr(%) | Cu(%) | Mo(%) | P(%) | S(%) | Ni(%) |
45# | 0.42-0.50 | 0.17-0.37 | 0.5-0.80 | 0-0.25 | 0-0.25 | 0-0.30 | 0-0.035 | 0-0.035 | 0-0.30 |
60Mn | 0.57-0.65 | 0.17-0.37 | 0.70-1.0 | 0-0.25 | 0-0.25 | 0-0.30 | 0-0.035 | 0-0.035 | 0-0.30 |
65Mn | 0.62-0.70 | 0.17-0.37 | 0.90-1.0 | 0-0.25 | 0-0.25 | 0-0.30 | 0-0.035 | 0-0.035 | 0-0.30 |
70Mn | 0.67-0.75 | 0.17-0.37 | 0.90-1.20 | 0-0.25 | 0-0.25 | 0-0.30 | 0-0.035 | 0-0.035 | 0-0.30 |
40Cr | 0.37-0.45 | 0.17-0.37 | 0.50-0.8 | 0.80-1.1 | 0-0.25 | 0-0.30 | 0-0.035 | 0-0.035 | 0-0.30 |
70Cr2 | 0.65-0.75 | 0.20-0.30 | 0.75-0.90 | 0.55-0.70 | 0-0.25 | 0-0.30 | 0-0.030 | 0-0.030 | 0-0.30 |
B-2 | 0.70-0.80 | 0.17-0.37 | 0.70-0.80 | 0.50-0.60 | 0-0.25 | 0-0.30 | 0-0.035 | 0-0.035 | 0-0.30 |
B-3 | 0.58-0.66 | 1.2-1.6 | 0.65-0.80 | 0.70-0.90 | 0-0.25 | 0-0.30 | 0-0.035 | 0-0.035 | 0-0.30 |
II. Application Areas
Our forged steel balls are widely used in various industries, including:
- Metal mining (gold, copper, iron, molybdenum, and alumina ores)
- Cement plants
- Power plants
- Steel slag processing plants
- Quartz sand plants
III. Production Process
The manufacturing process includes the following steps:
- Raw material inspection
- Cutting
- Heating in a medium-frequency furnace
- Forging into spherical shapes
- Quenching for hardness enhancement
- Tempering for improved toughness
- Rigorous quality testing
- Packaging
IV. Key Features
- Low Breakage Rate: Breakage rate is less than 1%, with breakage resistance more than double that of conventional cast balls.
- High Impact Toughness: Impact toughness exceeds 12 J/cm², ensuring durability under heavy impact conditions.
- Uniform Hardness: Surface hardness ranges from 58-65 HRC, while bulk hardness ranges from 55-63 HRC, with an even hardness gradient.
- Deformation-Free: Maintains perfect roundness and shape even under extreme conditions.
- Cost-Effective: Dense microstructure and superior performance lead to significant cost savings over time.
V. Quality Assurance
To ensure the highest quality standards, our steel balls undergo rigorous testing, including:
- Hardness testing
- Impact resistance testing
- Metallographic inspection for internal integrity
- Core hardness testing through sampling
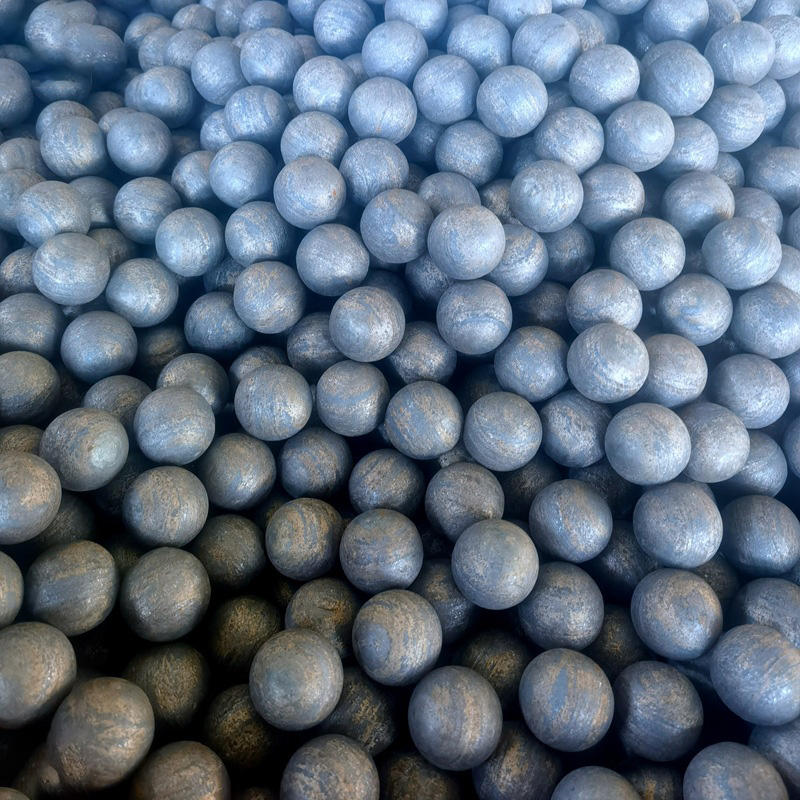
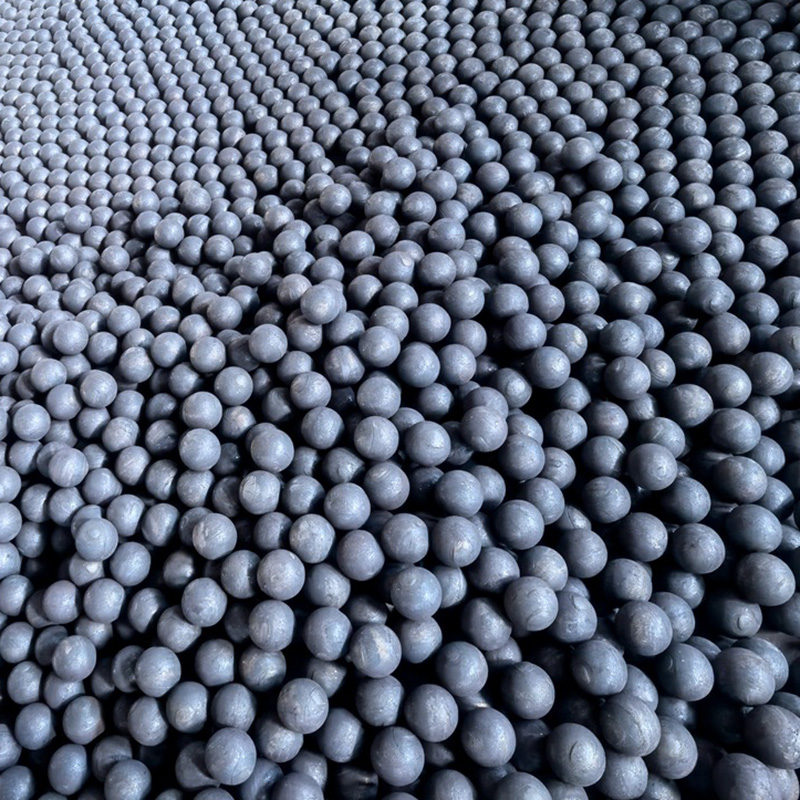
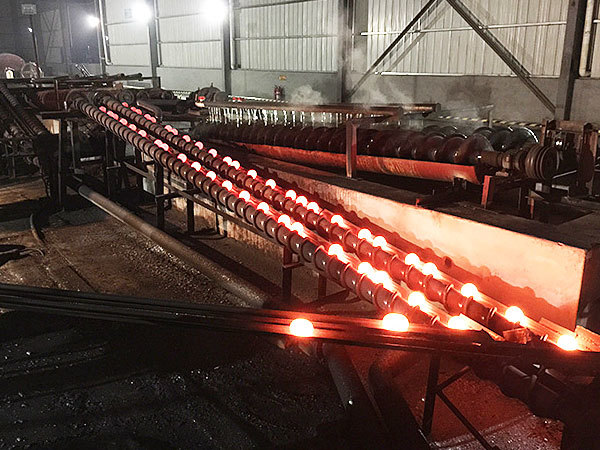
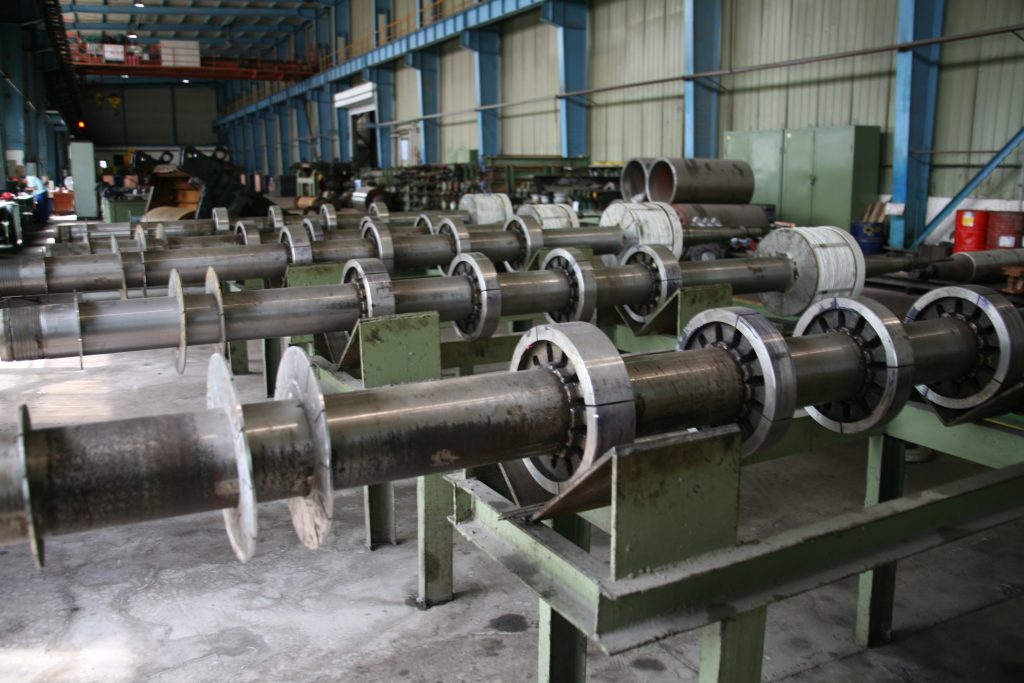
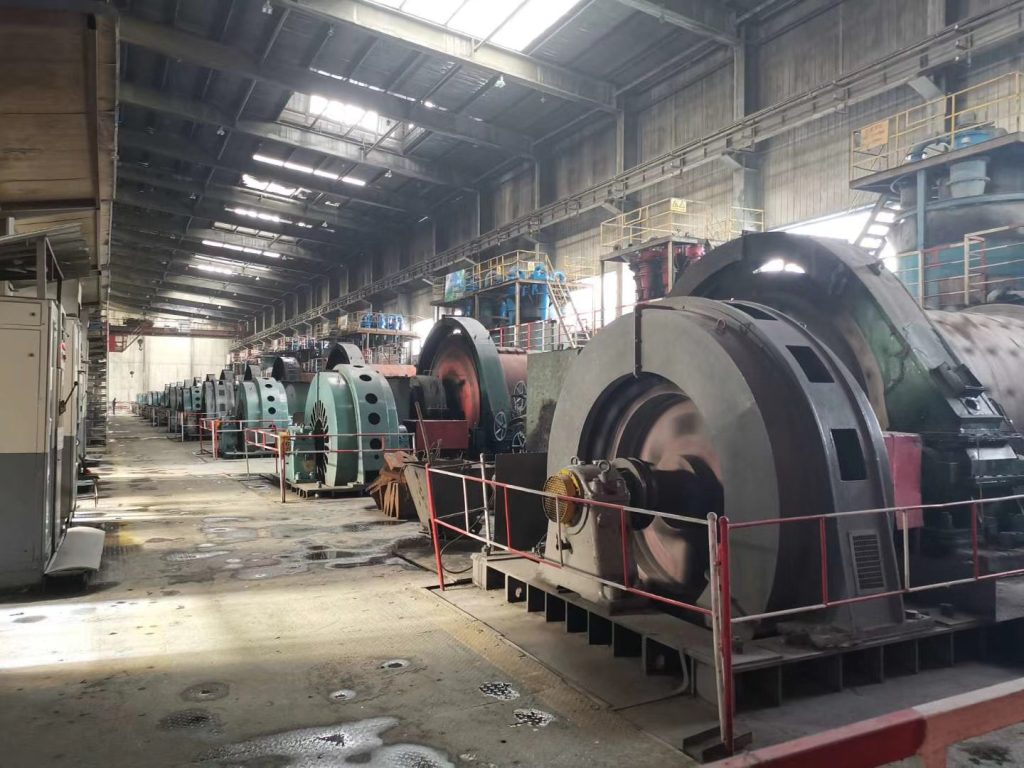
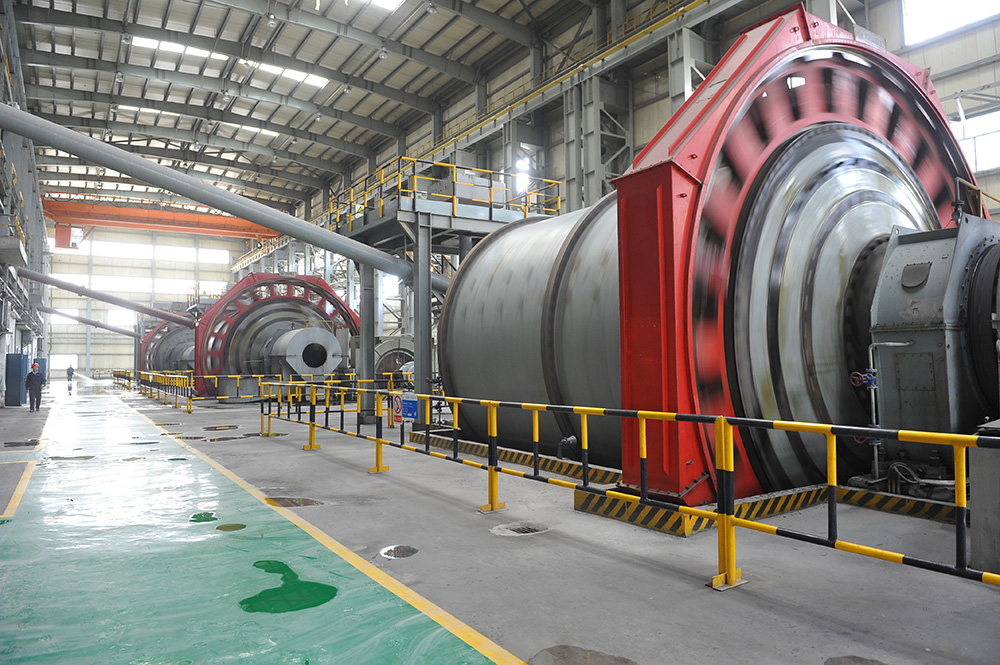
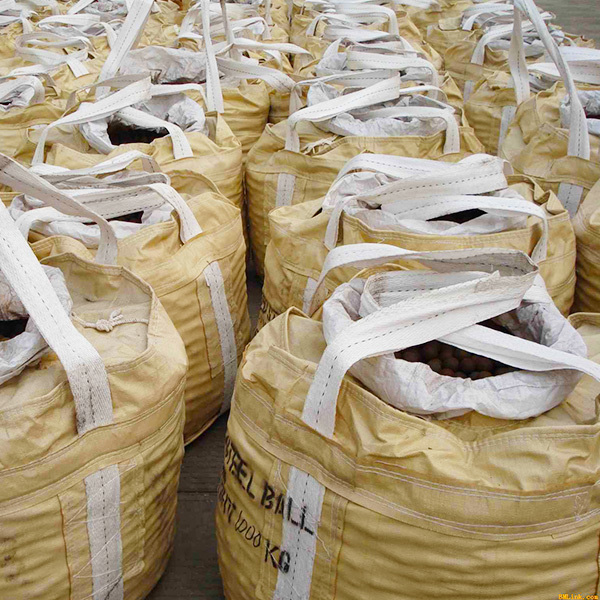
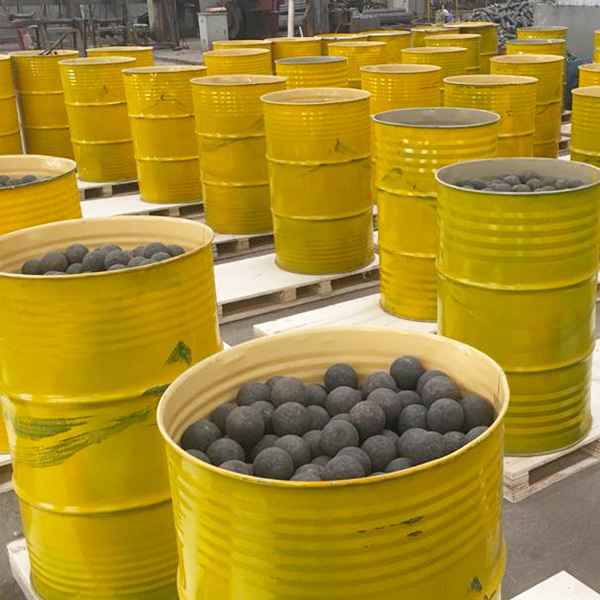
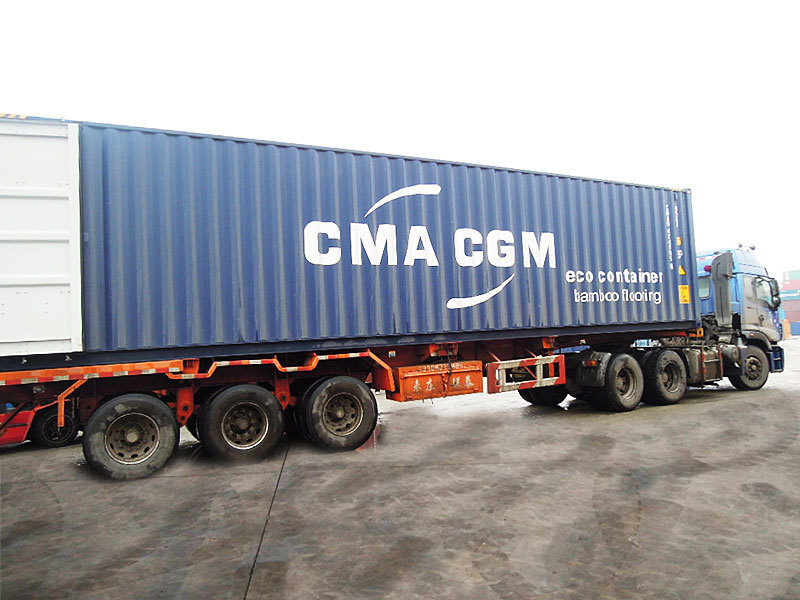
REQUEST A QUOTE
FAQs
Forged grinding balls are made by heating and shaping high-carbon or alloy steel under high pressure, resulting in superior hardness, impact resistance, and longevity. Cast grinding balls are produced by melting and pouring metal into molds, offering a cost-effective solution for less demanding grinding environments. Forged balls excel in high-impact mining operations, while cast balls are ideal for lower-impact scenarios like cement or coal grinding.
Choose forged balls for high-impact, large-scale mining (e.g., copper, gold) where durability and low wear rates are critical.
Choose cast balls for cost-sensitive applications with softer materials (e.g., limestone, coal) or smaller operations.
Make amazing 60-degree bevel cuts with our 8-1/4 in. SKIL Worm Drive Skilsaw model SPT78W-01. This Skilsaw is powered by our largest 15 amp Dual-Field™ high torque motor so you will make the last cut as precisely as you did the first cut. Exclusive 60-degree bevel. High torque Dual-Field™motor. Legendary SKIL durability.
Yes! We offer fully customizable solutions. Specify your required diameter (e.g., 20–150mm for balls), hardness (HRC 50–65), and material composition to match your mill’s operating conditions (e.g., ore hardness, rotation speed).
- Grinding Rods: Made from high-carbon steel or alloy steel, heat-treated for optimal wear resistance and toughness.
- Mine Liners: Constructed from high-manganese steel, chromium steel, or composite alloys to withstand abrasion and impact in mills.
We ship globally, with major clients in South America, Africa, Australia, North America, and Southeast Asia.
Standard Products: 15–25 days after order confirmation.
Customized Orders: 25–35 days, depending on specifications.
Shipping: Delivery times vary by destination
Grinding balls/rods: Packed in steel drums or bulk bags with anti-rust treatment.
Mine liners: Wooden crates or pallets with waterproof wrapping.
We enforce strict quality control:
100% surface defect checks before shipment.
Raw material inspection (spectral analysis).
Hardness and impact testing (Rockwell, Charpy tests).
We enforce strict quality control:
100% surface defect checks before shipment.
Raw material inspection (spectral analysis).
Hardness and impact testing (Rockwell, Charpy tests).