Mill Grinding Balls, Grinding Cylpebs and Grinding Rods
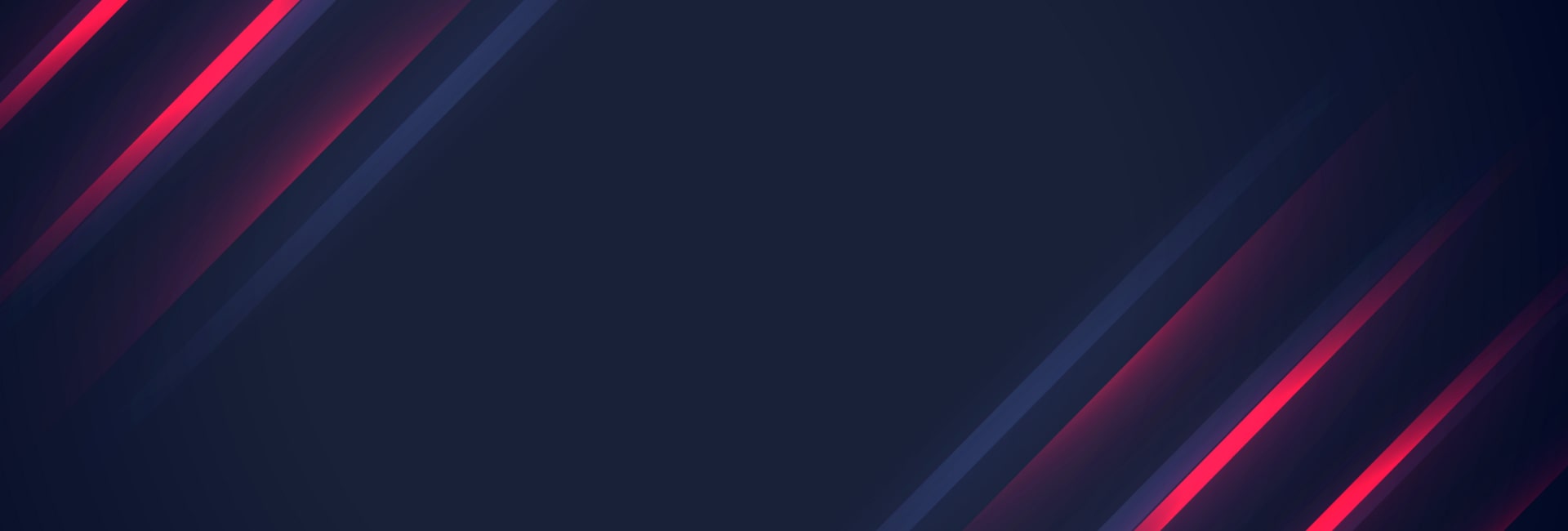
Forged Steel Ball Engineered for SAG Mills
PRODUCT PARAMETERS
- Type: Forged Steel Grinding Balls
- Diameters(mm): 100 mm to 165 mm (4” to 6.5”)
- Application: mining, cement production, power plants, chemistry industries
- High hardness
- Good wear resistance
- High impact toughness
- Rear earth grinding ball available (HRC up to 60-65)
Description
It is a forged steel ball specifically engineered for use in SAG mills.The grinding media balls can be delivered in diameters ranging from 100 mm to 165 mm (4” to 6.5”).
Diameters and Roundness:
Diameter (mm) | 30 | 40 | 50 | 60 | 70 | 80 | 90 | 100 | 110 | 120 | 125 | 150 |
Diameter roundness(mm) | ±2 | +3, -2 | +4, -3 | +5, -4 | ||||||||
Roundness(%) | ≤2 | ≤3 | ≤4 | ≤5 |
Technical Parameter
Material | Breakage rate | Hardness(HRC) | Impact value(J/cm²) | Drop times(times) | Micro structure |
45# | <1% | ≥45 | ≥12 | ≥8000 | M+C |
60Mn | <1% | ≥55 | ≥12 | ≥12000 | M+C |
65Mn | <1% | ≥58 | ≥12 | ≥12000 | M+C |
70Mn | <1% | ≥60 | ≥12 | ≥12000 | M+C |
40Cr | <1% | ≥55 | ≥12 | ≥12000 | M+C |
70Cr2 | <1% | ≥58 | ≥12 | ≥12000 | M+C |
B-2 | <1% | ≥58 | ≥12 | ≥15000 | M+C |
B-3 | <1% | ≥60 | ≥12 | ≥15000 | M+C |
Chemical composition
Material | C(%) | Si(%) | Mn(%) | Cr(%) | Cu(%) | Mo(%) | P(%) | S(%) | Ni(%) |
45# | 0.42-0.50 | 0.17-0.37 | 0.5-0.80 | 0-0.25 | 0-0.25 | 0-0.30 | 0-0.035 | 0-0.035 | 0-0.30 |
60Mn | 0.57-0.65 | 0.17-0.37 | 0.70-1.0 | 0-0.25 | 0-0.25 | 0-0.30 | 0-0.035 | 0-0.035 | 0-0.30 |
65Mn | 0.62-0.70 | 0.17-0.37 | 0.90-1.0 | 0-0.25 | 0-0.25 | 0-0.30 | 0-0.035 | 0-0.035 | 0-0.30 |
70Mn | 0.67-0.75 | 0.17-0.37 | 0.90-1.20 | 0-0.25 | 0-0.25 | 0-0.30 | 0-0.035 | 0-0.035 | 0-0.30 |
40Cr | 0.37-0.45 | 0.17-0.37 | 0.50-0.8 | 0.80-1.1 | 0-0.25 | 0-0.30 | 0-0.035 | 0-0.035 | 0-0.30 |
70Cr2 | 0.65-0.75 | 0.20-0.30 | 0.75-0.90 | 0.55-0.70 | 0-0.25 | 0-0.30 | 0-0.030 | 0-0.030 | 0-0.30 |
B-2 | 0.70-0.80 | 0.17-0.37 | 0.70-0.80 | 0.50-0.60 | 0-0.25 | 0-0.30 | 0-0.035 | 0-0.035 | 0-0.30 |
B-3 | 0.58-0.66 | 1.2-1.6 | 0.65-0.80 | 0.70-0.90 | 0-0.25 | 0-0.30 | 0-0.035 | 0-0.035 | 0-0.30 |
Advantages of Forged Steel Balls for SAG Mills
Our factory is a leading Chinese manufacturer of forged steel balls, specializing in the R&D and production of grinding media. Its forged steel balls enjoy a strong reputation in domestic and international markets, particularly in industries such as mining, cement, and power generation.
1. Advanced Forging Technology and Processes
– Fully Automated Production Lines:
The factory has fully automated forging lines combined with modern heat treatment technologies (e.g., continuous quenching and tempering processes), ensuring uniform and dense internal grain structures in the steel balls. This achieves an optimal balance between hardness and toughness.
– Proprietary Technologies:
Our factory holds multiple forging process patents (e.g., its “Energy-Saving Hot-Rolled Steel Ball Production Line”), improving energy efficiency while enhancing product consistency.
2. High-Quality Material Selection
– High-Purity Alloy Steel:
Premium high-carbon steels (e.g., 60Mn, 65Mn) and alloy steels (e.g., B2, B3) are used, with precise chemical composition control to ensure high wear resistance and impact toughness.
– Rare Earth Element Modification:
Some products incorporate rare earth elements to refine grain structures and increase surface hardness (up to HRC 60-65), extending service life.
3. Rigorous Quality Control Systems
– End-to-End Testing:
Strict inspection protocols are applied from raw material intake to final product delivery, including spectral analysis, hardness testing (Rockwell scale), impact testing, and metallographic analysis. This eliminates defects like internal cracks or porosity.
– International Certifications:
The company holds ISO 9001 (Quality Management System) and ISO 14001 (Environmental Management System) certifications. Its products comply with global standards (e.g., ASTM, DIN) and are exported to over 50 countries.
4. Significant Economic Benefits
– Low Wear Rates:
Our forged steel balls exhibit 30%-50% lower wear rates compared to standard cast balls in both wet and dry grinding conditions, reducing downtime for replacements.
– Optimized Cost per Ton of Ore:
Although individual balls have a higher upfront cost, their extended lifespan and lower wear translate to significant savings in total ore processing costs (client-reported savings exceed 20% in some mining operations).
5. Customization and Product Diversity
– Wide Size Range:
Offers steel balls with diameters ranging from 20mm to 150mm, catering to various ball mill specifications (e.g., large semi-autogenous grinding mills).
– Scenario-Specific Adaptations:
Adjusts heat treatment processes based on client requirements (e.g., ore hardness, mill rotation speed) to deliver tailored products with enhanced hardness or toughness.
6. Environmental Sustainability
– Energy-Efficient Production:
Utilizes waste heat recovery technologies to reduce energy consumption during forging, aligning with green manufacturing practices.
– Circular Economy:
Worn steel balls are 100% recyclable, minimizing resource waste and supporting sustainable mining practices.
7. Market Competitiveness and Client Recognition
– Global Presence:
Exports to mining hubs such as South America, Africa, and Australia, with long-term partnerships with global mining giants.
– Industry Reputation:
Praised by clients as “one of the most cost-effective grinding media suppliers” for outstanding performance in projects like Chilean copper mines and Australian iron ore operations.
Unique Advantages Over Competitors
– Technical Barriers:
Fully automated production lines and patented processes ensure consistent quality at scale, which smaller competitors struggle to replicate.
– Cost Efficiency:
Economies of scale in procurement and production management enable competitive pricing.
– After-Sales Support:
– Provides value-added services like technical consulting and wear analysis to optimize clients’ grinding efficiency.
– Advanced forging technology guarantees superior performance;
– Strict quality control and customization capabilities meet diverse client needs;
– Cost efficiency and global reach secure market leadership.
For mining and industrial users prioritizing long-term efficiency, our forged steel balls offer an optimal balance of durability, economy, and reliability. For detailed data (e.g., wear rate test reports or case studies), direct consultation with their technical team is recommended.
REQUEST A QUOTE
FAQs
Forged grinding balls are made by heating and shaping high-carbon or alloy steel under high pressure, resulting in superior hardness, impact resistance, and longevity. Cast grinding balls are produced by melting and pouring metal into molds, offering a cost-effective solution for less demanding grinding environments. Forged balls excel in high-impact mining operations, while cast balls are ideal for lower-impact scenarios like cement or coal grinding.
Choose forged balls for high-impact, large-scale mining (e.g., copper, gold) where durability and low wear rates are critical.
Choose cast balls for cost-sensitive applications with softer materials (e.g., limestone, coal) or smaller operations.
Make amazing 60-degree bevel cuts with our 8-1/4 in. SKIL Worm Drive Skilsaw model SPT78W-01. This Skilsaw is powered by our largest 15 amp Dual-Field™ high torque motor so you will make the last cut as precisely as you did the first cut. Exclusive 60-degree bevel. High torque Dual-Field™motor. Legendary SKIL durability.
Yes! We offer fully customizable solutions. Specify your required diameter (e.g., 20–150mm for balls), hardness (HRC 50–65), and material composition to match your mill’s operating conditions (e.g., ore hardness, rotation speed).
- Grinding Rods: Made from high-carbon steel or alloy steel, heat-treated for optimal wear resistance and toughness.
- Mine Liners: Constructed from high-manganese steel, chromium steel, or composite alloys to withstand abrasion and impact in mills.
We ship globally, with major clients in South America, Africa, Australia, North America, and Southeast Asia.
Standard Products: 15–25 days after order confirmation.
Customized Orders: 25–35 days, depending on specifications.
Shipping: Delivery times vary by destination
Grinding balls/rods: Packed in steel drums or bulk bags with anti-rust treatment.
Mine liners: Wooden crates or pallets with waterproof wrapping.
We enforce strict quality control:
100% surface defect checks before shipment.
Raw material inspection (spectral analysis).
Hardness and impact testing (Rockwell, Charpy tests).
We enforce strict quality control:
100% surface defect checks before shipment.
Raw material inspection (spectral analysis).
Hardness and impact testing (Rockwell, Charpy tests).